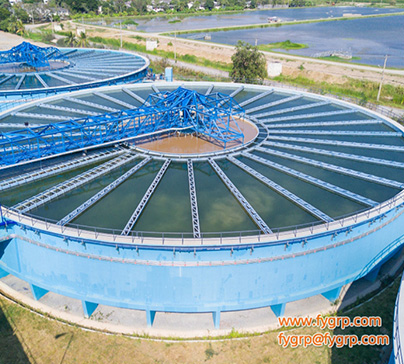
Описание процесса изготовления вышки FYGRP®
Оборудование FYGRP изготовлено с использованием новейшей версии проволочного станка с ЧПУ. Конкретные производственные процессы заключаются в следующем:
1. Выбор материала: Мы используем виниловые эфирные смолы на основе прошлого опыта, усиливающий материал выбирает E - стекло непрерывной ровницы.
2. Процесс подготовки
(1) Внимательно прочитайте инструкции по проектированию, обратите внимание на ключевые вопросы, такие как выбор сырья, размер каждой детали, выбор формы и ламинарный дизайн.
(2) Отладка оборудования. Прежде всего, тщательно проверьте, работает ли оборудование и рабочие компоненты нормально, в частности, засорен ли двухкомпонентный насос для отверждения смолы, соответствует ли соотношение требованиям конструкции, чтобы обеспечить стабильную работу и точность работы оборудования, например, изготовление футеровки, намотки, отделки, разминки и так далее.
(3) Чистые формы. Поверхность формы должна быть свободной от выбоин, пыли, обломков и других принадлежностей. Поверхность формы должна быть гладкой. В случае возникновения проблем, пожалуйста, своевременно отремонтируйте и отремонтируйте.
(4) Упаковка полиэфирной пленки. Для облегчения отформатирования поверхность формы должна быть покрыта слоем полиэфирной пленки. Ширина перекрытия пленки составляет от 1 до 2 см, толщина около 40 м. Требуется, чтобы пленка была без повреждений, без складок, обе стороны гладкие и чистые. Качество пленки соответствует требованиям GB13950 - 1992.
3.Формирование облицовки кузова. В зависимости от структуры интерьер делится на внутренний и переходный слои. Этот слой играет в основном антикоррозионную и непроницаемую роль.
(1) Приготовление смолы для футеровки. Интерьерная смола смешивается отделом контроля качества в соответствии с текущей рабочей средой и температурой, разработанной системой формулы смолы, количество ингредиентов должно разумно контролироваться в соответствии с графиком производства. Когда ситуация на месте меняется, производственный отдел должен своевременно скорректировать формулу и подготовить подходящую смолу в соответствии с новой формулой.
(2) Изготовление футеровки в соответствии с порядком ламинации конструкции. Стальной штамп, изготовленный из винтовки Venus. Содержание смолы в футеровке высокое, с хорошим антикоррозионным и непроницаемым эффектом. Содержание смолы в футеровке 90 + 2%, содержание смолы в переходном слое 80%.
(3) Проверка процесса. После нанесения каждого слоя в соответствии с требованиями конструкции оператор должен провести предварительную проверку качества, достигла ли футеровка проектной толщины, есть ли разница в клее или локальное подвешивание, есть ли белые пятна или пузырьки, и, если да, немедленно сообщить и принять меры по обработке.
(4) Обложка глубоко отверждена и смоделирована.
4. Формирование и укрепление верхней и нижней крышек. Заглушка делится по структуре на футеровки и структурные слои.
(1) Процесс формования и сырье для футеровки крышки идентичны корпусу. Огнестрельное формование, высокое содержание смолы. После нанесения покрытия на голову проводится глубокое отверждение.
(2) Использовать попеременное строительство головных конструкционных слоев, струйной ровницы и тканевой ровницы. Во время укладки каждый слой ровницы должен наносить соответствующее натяжение и надлежащим образом перекрываться, а пузырьки многократно прокручиваются комбинированными роликами, чтобы обеспечить полное проникновение стекловолокна в смолу. Каждый усиленный слой должен достигать проектного содержания смолы.
(3) Технологическая проверка, глубокое обслуживание, снятие модели.
5. Сборка
(1) отвержденные футеровки тела и головы размножаются и режутся до размеров, указанных в проектной документации.
(2) Обложка корпуса клапана стыкована с уплотнением с помощью сборочного кольца, отрегулирована до номинального диаметра 30 мм, вставлено сборочное кольцо в футеровку корпуса клапана, расширяется до номинального диаметра 15 мм, нижняя крышка помещена в открытую часть сборочного кольца, медленно расширяется сборочное кольцо, Измеряйте периметр футеровки и диаметр 3 точек (равномерное распределение) до тех пор, пока не будут выполнены стандартные требования.
(3) Нанесите наружный усиленный слой стыковочного соединения, отполируйте область стыка, используйте ступенчатый тип (увеличение ширины), чтобы смазать внешний разъем изнутри наружу. Ширина самого внешнего слоя не менее 500 мм. После завершения общего укрепления внутренние швы склеиваются облицовочной смолой и коротким войлочным покрытием, а слоистое давление по ступенькам (увеличение ширины) наружно и изнутри.
(4) Проверка процедуры.
6. Общее укрепление
(1) Соедините собранную оболочку оборудования с волокнистой намоткой с ЧПУ, отполируйте и отремонтируйте внешнюю поверхность корпуса. Пробурите отверстие в сопле футеровки и надувайте его, чтобы обеспечить окружность футеровки.
(2) Местное укрепление зоны концентрации напряжений на нижней крышке и рулевом узле кузова с помощью короткого войлока. Регулируйте угол намотки и угол намотки головы, чтобы соответствовать характеристикам концентрации напряжений головы. Ширина упаковки нижней крышки более 250 мм, высота упаковки тела 400 мм.
(3) Использовать один высокий и более трех, задний оборот, передний спрей. Чередованное распыление ровницы, кольцевого обруча и скрещение, регулировка скорости прокладки и натяжения волокон для обеспечения содержания смолы в стенке резервуара. Нижняя поверхность крышки устройства с наружным наклонным днищем не перпендикулярна оси оборудования, регулирует оборудование для намотки и параметры намотки, длина скрещения в общем укреплении больше длины тела оборудования, обернутая ровня на верхней и нижней крышках оборудования, чтобы сформировать намотку бутонов.
(4) Проверка процесса, глубокое отверждение.
7. Сборочные сопла. В соответствии с чертежами отметьте местоположение, откройте и установите сопло.
8. Внешний защитный слой. После завершения общего производства (включая установку аксессуаров) наносите защитный слой, анти - стареющие гелевые покрытия смолы и ультрафиолетовые поглотители и пластификаторы.
9 Осмотр доставки.